Production Planning and Control
Software empowers you to take charge of your production processes with advanced planning and control features. Create detailed production schedules based on demand forecasts, material availability, and work center capacity. Manage manufacturing orders efficiently, tracking progress, material consumption, and labor costs in real-time. Define work orders for specific tasks, ensuring clear assignments and accountability. Utilize the Bill of Materials (BOM) module to define and manage product structures, ensuring accurate material requirements. Optimize production flow with routing capabilities, specifying the sequence of operations and work centers involved. Empower your shop floor workers with real-time instructions, production tracking, and data capture capabilities through the Shop Floor Control module.
Production Scheduling
Plan your production with precision. Create detailed production schedules that consider demand forecasts, available materials, and the capacity of your work centers. This ensures efficient resource allocation and timely production.
Manufacturing Order Management
Gain complete control over your manufacturing orders. Track progress in real-time, monitor material consumption, and keep an eye on labor costs. This granular visibility allows for proactive management and optimized production workflows.
Work Order Management
Define and assign work orders for specific tasks within the production process. Ensure clear assignments, track progress, and maintain accountability for each step in the manufacturing process.
Production Floor Control
Empower your production floor workers with digital tools. Provide them with real-time instructions, enable them to track production progress, and capture data directly from the floor. This streamlines operations and improves efficiency.
Manufacturing ERP Software to Streamline Production
A comprehensive manufacturing ERP software designed to streamline your production processes, optimize resource utilization, and boost overall efficiency. Our software empowers manufacturing businesses of all sizes to gain complete control over their operations, from production planning and inventory management to quality control and financial reporting. With its user-friendly interface, powerful features, and seamless integrations, [Product Name] enables you to make data-driven decisions, reduce costs, and enhance productivity, driving your manufacturing business towards greater success.

PRODUCTION & MANUFACTURING ERP SOFTWARE


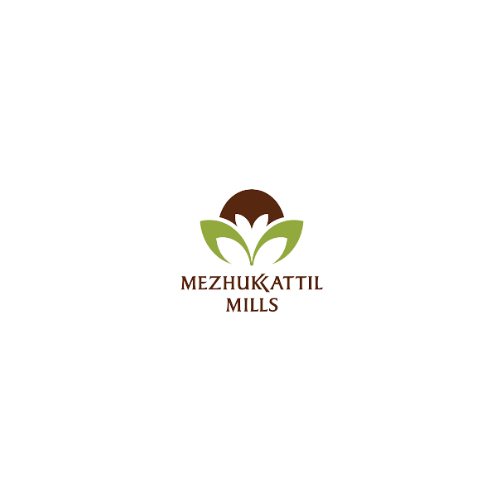

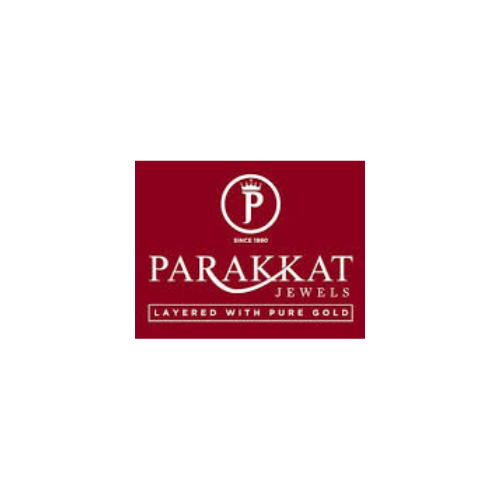


Inventory and Resource Optimization
Optimize inventory levels and resource utilization with [Product Name]'s integrated tools. Gain real-time visibility into inventory levels, track stock movements, and automate replenishment to ensure material availability for production. Leverage the MRP (Material Requirements Planning) module to plan and manage material procurement based on production needs and lead times, minimizing stockouts and reducing carrying costs. Implement quality control measures at every stage of production, managing quality alerts and tracking corrective actions to maintain high product standards. Schedule preventive maintenance, track equipment performance, and manage repairs efficiently with the Maintenance Management module, minimizing downtime and extending the lifespan of your valuable assets.
Inventory Management
Maintain optimal inventory levels with real-time tracking and automated replenishment. Minimize stockouts, reduce carrying costs, and ensure timely material availability for production.
MRP (Material Requirements Planning)
Plan and manage material procurement efficiently. The MRP module ensures you have the right materials at the right time, minimizing delays and optimizing inventory levels.
Quality Control
Implement robust quality control measures throughout your production process. Track quality metrics, manage inspections, and address deviations to ensure consistent product quality and customer satisfaction.
Maintenance Management
Keep your equipment running smoothly with preventive maintenance scheduling, performance tracking, and efficient repair management. Minimize downtime and extend the lifespan of your valuable assets.
Finance and Accounting
Seamlessly integrates with your financial and accounting processes, providing complete visibility into manufacturing costs and profitability. Track expenses, manage budgets, and generate financial reports with ease. Gain insights into project costs, analyze profit margins, and make informed decisions to optimize financial performance. The integrated accounting module ensures accurate cost accounting, streamlined invoicing, and efficient financial management.
Expense Tracking
Gain a clear view of your manufacturing expenses. Track costs related to materials, labor, overheads, and more. This detailed tracking enables better cost control and informed decision-making.
Budget Management
Create and manage budgets for your manufacturing operations. Track actual costs against planned budgets, monitor variances, and make necessary adjustments to maintain financial control.
Financial Reporting
Generate comprehensive financial reports with ease. Gain insights into your overall financial performance, including profitability analysis, cost breakdowns, and key financial metrics.
Cost Accounting
Ensure accurate cost accounting for your manufacturing processes. Track costs at each stage of production, analyze cost variances, and identify areas for optimization to improve profitability.
Frequently Asked Questions
-
What ERP solutions does Catalist offer?Catalist offers comprehensive ERP software designed to meet the specific needs of businesses in the Construction and Contracting, Manufacturing and Production, and Wholesale and Retail sectors.
-
What are the key features of Catalist Construction ERP software?treamline your construction projects and boost profitability with our ERP software, featuring: Real-time Project Tracking: Stay on top of project progress and make informed decisions. Accurate Cost Estimation: Control costs and maximize profitability. Efficient Resource Management: Optimize the use of materials, labor, and equipment. Simplified Billing: Generate accurate invoices quickly and easily. Improved Collaboration: Enhance communication and coordination among project stakeholders.
-
What are the key features of Manufacturing ERP solutions?Core Manufacturing Functions: Production Planning and Scheduling: This is the heart of the system. It includes Master Production Scheduling (MPS), Material Requirements Planning (MRP), Capacity Planning, and shop floor control. It helps plan production, optimize resource allocation, and manage production schedules. Materials Management: Covers inventory control, purchasing, receiving, and managing raw materials, components, and finished goods. It often includes features like demand forecasting, inventory optimization, and supplier management. Shop Floor Control: Manages and tracks production activities on the shop floor, including work order management, production tracking, data collection, and quality control. Bill of Materials (BOM) Management: Centralized management of product structures, components, and sub-assemblies. This is crucial for accurate production planning and costing. Quality Management: Includes quality control, inspection, non-conformance tracking, and corrective actions. Helps ensure product quality and compliance with standards. Cost Management: Tracks and analyzes manufacturing costs, including direct materials, direct labor, overhead, and other expenses. Provides insights into cost drivers and profitability.
-
What are the services provided by Catalist ?Catalist Business Solutions offers a broader range of consulting and implementation services related to ERP: ERP Strategy & Planning: Helping businesses define their ERP needs, select the right software, and develop an implementation plan. ERP Implementation: Managing the entire implementation process, from project planning and configuration to data migration and user training. Customization & Development: Tailoring ERP solutions to meet specific business requirements. Integration: Connecting ERP systems with other business applications. Training & Support: Providing comprehensive training and ongoing support to users. Business Process Re-engineering: Helping businesses optimize their processes to maximize the benefits of their ERP system. Organizational Change Management: Assisting businesses in managing the organizational changes that come with implementing a new ERP system. Post-Implementation Support: Providing ongoing support and maintenance to ensure the ERP system continues to meet the business's needs.
-
How to get a consultation or demo of Catalist ERP software products?For inquiries, please contact us at +91 7736293665 or info@catalistindia.in. You can also chat with a representative on our website.

Customizable Reports
Gain deeper insights into your manufacturing operations with customizable reports. Generate reports tailored to your specific needs, analyzing data on production performance, inventory levels, financial metrics, sales data, and more.
Interactive Dashboards
Visualize key performance indicators (KPIs) with interactive dashboards. Monitor real-time data, track progress towards goals, and identify areas for improvement with intuitive visualizations.
Traceability
Ensure complete traceability of materials and products throughout your manufacturing process. Track every step from raw materials to finished goods, ensuring compliance with regulations and enabling efficient recalls if necessary.
Integrations
Seamlessly integrate with CRM platforms, project management tools, e-commerce platforms, and more to create a unified data ecosystem and streamline workflows across your organization.
Reporting, Analytics, and Integrations
Make data-driven decisions with our ERP's powerful reporting, analytics, and integration capabilities. Generate customizable reports on all aspects of your manufacturing operations, from production performance and inventory levels to financial metrics and sales data. Visualize key performance indicators (KPIs) on interactive dashboards, providing real-time insights into your business. Trace materials and products throughout the manufacturing process, ensuring compliance and enabling efficient recalls. Seamlessly integrate with other business systems, such as CRM platforms, project management tools, and e-commerce platforms, to create a unified data ecosystem and streamline workflows across your organization.